As human beings, we are very vulnerable to environmental conditions, especially those in the stratosphere. Unlike cockroaches (which seem oddly equipped for pretty much anything), humans cannot survive in extremely low or extremely high ambient pressures or temperatures. Perhaps the best minds of our generation didn’t immediately think “how can I be more like this indestructible insect”, but nevertheless technological advancements have helped us get one step closer to their tenacity…at least in stratospheric conditions. Technology does not stand still though and is constantly improving and with it, we’re given more choices and variety in environmental control systems.
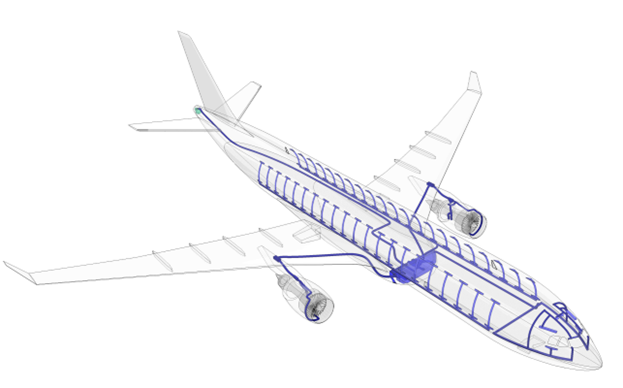
When designing environmental control systems (ECS), it is very important to understand that the top priority of these systems is to provide safety and comfort under absolutely any conditions, whether flying over the Sahara Desert or Alaska. We are talking about a minimum of 75 kPa and 20-24 °C. Relative humidity should range from 15 to 60% [1].
The ECS is usually split in one air conditioning machine (ACM) pack per engine. The ACM size is dictated by the ventilation requirement of 6 (g/s)/pax minimum (e.g. 1.2 kg/s minimum for the 200 pax capacity of A320; some 2 kg/s is the typical design value). This air can be taken both from the engine and through separate air intakes (but that’s a completely different story).
This brings us to the classification of systems. Aviation has been using one type of system for many years, specifically the convective bleed air type. It is reliable, efficient, and proven to work over the years.
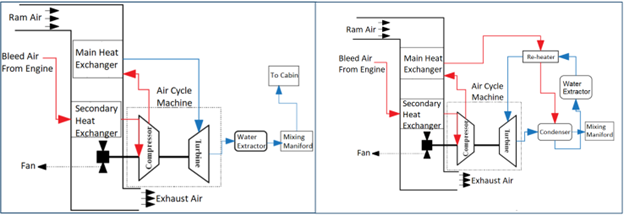
This kind of system can be classified into either a Low-Pressure Water Separation System (LPWS) or High-Pressure Water Separation System (HPWS).
The difference between LPWS and HPWS is the water extraction loop; consisting of a reheater and condenser. Although LPWS have fewer components and a lower weight, the absence of the water extraction loop unit becomes the limiting factor. The absence of this loop can lead to icing near the turbine unit. This icing is not a desirable effect and thus, the HPWS became the better choice and is used commercially on a large scale [3].
So, how does compressed and heated air get into the cabin? Let’s figure it out.
![Figure 3 – Bleed pneumatic system (from Boeing) [1]](https://xlera8.com/wp-content/uploads/2022/11/choosing-the-best-environmental-control-system-when-designing-an-aircraft-2.png)
By taking air from the engine, we also reduce its thrust. To compensate for the loss of thrust, we can only slightly increase the fuel consumption in the engine. Air is bled from the main engine compressors through a flow control valve at around 250 kPa; it is very hot (>200 ºC) because of the adiabatic compression heating. As pressure and temperature of bleeding depends on compressor stage and spinning rate, this pressure is regulated by having two or three bleedings at different stages and control valves (see Fig. 2). The hot bled air always requires cooling before entering the cabin, but a simple heat exchanger (HE) with outside air is not efficient (a big HE is needed to cool that amount of air from 200 ºC to 20 ºC, particularly at low altitudes). To guarantee that bled air can be safely piped from the engine through the fuselage to the air-cycle machine and de-icing system, a heat exchanger (pre-cooler) in the engine cools bled air from the compressor (at >200 ºC) to some 180 ºC (450 K).
Next, the air enters the air conditioning machine which cools, relieves pressure, and regulates moisture. The air is then mixed with the air from the cabin and moves through the air distribution system back to the passengers. This system is designed in such a way that air exits at a speed not higher than 2 m/s in each nozzle.
Design of Environmental Control System
To recap, the ECS consists of 3 parts: the air intake system from the engine, air-cycle machine, and air distribution system.
In the last ECS (Figure 1), it was necessary to take into account the dimensions and speed of the airflow so that at the outlet it does not exceed 2 m/s. This gives us the opportunity to determine the pressure and temperature losses in the pipeline.
![Figure 4 – Bleed air ECS schematic view [4] and ECS model in AxSTREAM MBSE](https://xlera8.com/wp-content/uploads/2022/11/choosing-the-best-environmental-control-system-when-designing-an-aircraft-3.png)
The air-cycle machine (ACM) is based on an inverse Brayton refrigeration cycle. Pre-cooled air from the bleed system is further cooled in a primary heat exchanger (Fig. 3) down to some 110 ºC, and then enters a compressor with a pressure ratio around π=1.8 that raises the air to 210 ºC. A second heat exchanger then lowers the temperature again to some 100 ºC. Pressure losses in these compact heat exchangers are high (20..40 kPa). Afterwards, air passes through a turbine and exits at about 5 ºC, to be mixed with some hotter bled air at around 100 ºC to get the 10…35 ºC (it depends on operation phase) needed to keep the cabin air at around 22 ºC at all times, accounting for internal heat release (passengers and equipment), outside heat gain and loses, and air recirculation.
Such complex modeling allows us to track the desired parameters with changes in the boundary conditions (and even over time) at any point in the system and determine at what specific values of the parameters the system will be most efficient.
Electrical Environmental Control System
Despite the comprehensive use and reliability of the convective system, Boeing recently introduced a completely new (electric) type of system. They also electrolyzed several other important aircraft systems and introduced the new Boeing 787 to the world.
The electrical system is very similar to the convective system. The only difference is that it takes air for conditioning from additional air intakes where the air is then compressed using electric compressors instead of the engine.
![Figure 5 – External air sources in Boeing 787 [5].](https://xlera8.com/wp-content/uploads/2022/11/choosing-the-best-environmental-control-system-when-designing-an-aircraft.jpg)
Additional electrical generators on the engines supply the ECS power (hundreds of kilowatts) to drive the electrical compressors and electric heaters for de-icing (electro-thermal heater mats attached to the aircraft slats). There are two ECS compressors on each pack, which are 0.3 m in diameter, run at 40…50 thousand rpm on air bearings, and have a total pressure ratio of π=5 (on each pack), taking ram air (at cruise, from 20 kPa to 100 kPa), and delivering it at 90 ºC instead of the 180 ºC in conventional bleed-air ECS. This AE-ECS adds some 200 kg on airliners (and some maintenance costs) but saves roughly 5% fuel (maybe 5000 kg). Higher humidity in the passenger cabin is possible because of the use of composites (which do not corrode).
The operation cost in the nominal ECS is the work spent in compressing the bled air, which is:

In the electrical system for 1 kg/s of air, 125 kW is needed to increase the pressure to 1 atm. At the same time, the outlet temperature is 90 °C lower than in a blind air system, which is accompanied by lower thermal loads and the absence of the need for an additional precooler. Also, simply by adjusting the power in the compressor, you can control the pressure in the cabin. And such a relatively low pressure from the compressor can be justifiably a smaller path for the passage of air, that is, lower losses, mass, etc. The system itself is simpler, which in the future may be cheaper to maintain. The source of electricity can be not only from engine generators. It can also be a fuel cell or a battery, which can also be calculated in AxSTREAM MBSETM.
Interested in exploring 1D software for your environmental control system? Reach out to us for a free consultation by emailing [email protected]
References:
- Coinsmart. Europe’s Best Bitcoin and Crypto Exchange.Click Here
- Platoblockchain. Web3 Metaverse Intelligence. Knowledge Amplified. Access Here.
- Source: https://blog.softinway.com/choosing-the-best-environmental-control-system-when-designing-an-aircraft/